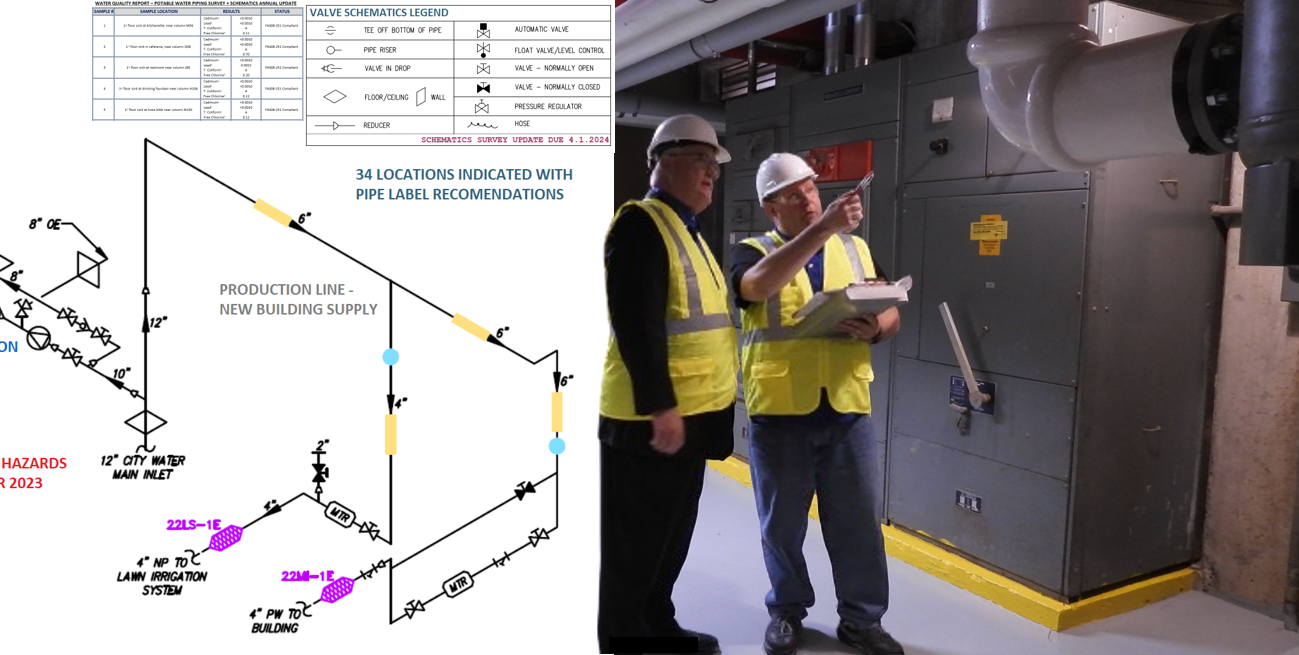
For many manufacturing companies with large, complex facilities considering tools and methods to avoid downtime, the importance of maintaining accurate and up-to-date piping schematics cannot be overstated. In this article, we delve into the myriad benefits of periodically updating piping schematics and keeping digital copies of these schematics saved on company servers, focusing on how it can bridge the gap for understaffed facility management teams. By enabling remote navigation, proactive planning, and timely maintenance, updated schematics play a crucial role in preventing emergency situations, minimizing failures, and optimizing operational efficiency, insuring a positive and substantial Return on Investment.
I. Remote Navigation:
Updating and digitizing piping schematics allows remote facility managers to navigate the entire system without being physically present. Remote monitoring tools can be integrated with the schematics, providing real-time insights into the condition of critical piping systems.
A. Enhanced Visibility:
- Digitized CAD schematics of piping layouts enable remote teams to navigate through the facility virtually and oversee multiple facilities at once.
- Access to accurate and detailed schematics facilitates quick identification of pipe routing and connections.
B. Time and Cost Savings:
- Reduced need for on-site presence results in cost-effective operations.
- Remote navigation minimizes travel time and expenses for facility management teams.
C. Real-Time Monitoring:
- Integration with new and emerging sensor technologies can allow for real-time intel on pipe conditions, including leak detection or pressure monitoring.
- Remote access enables facility managers to immediately respond to anomalies and dispatch their onsite staff directly to the source, preventing potential issues.
D. ROI Example: Sarah, the Remote Facility Manager
- Sarah, a facility manager, receives an alert about a potential issue in a crucial pipeline. Using the digital, recently updated piping schematics remotely, she identifies the problem, orders necessary parts, and guides on-site technicians to address the issue promptly. Downtime is minimized, resulting in cost savings and increased operational efficiency.
II. Proactive Planning:
Before you can digitize your up-to-date piping schematics, they will need to be manually updated by having staff or an independent contractor visually survey every inch of piping in your facility. Not only will this produce as-installed, up-to-date, and incredibly accurate schematics, but the process will also facilitate the identification of wear and tear, corrosion, or potential weak points in the piping systems. The surveyor will maintain a record of discovered issues and deliver them along with the drawings to the facility management team.
A. Predictive Maintenance:
- Early detection of wear and tear through the process of updating piping schematics aids in predictive maintenance.
- Proactively addressing potential issues minimizes downtime by pinpointing undetected and unknown issues early on and extends equipment lifespan.
B. Risk Mitigation:
- Identification of weak points and vulnerable areas allows for targeted risk mitigation strategies, including replacing old valves or removing dead legs.
- Proactive planning reduces the likelihood of catastrophic failures just as gas leaks and associated risks such as legionella in the potable water system.
C. Optimized Resource Allocation:
- Strategic planning based on updated schematics ensures efficient resource allocation, particularly of funds to pay for preventative maintenance and staffing.
- Prioritization of maintenance tasks based on criticality enhances operational resilience.
D. ROI Example: James, the Maintenance Technician
- During the survey to update the piping schematics, the contracted surveyor discovered a broken valve on the line that supplies a key machine in the manufacturing assembly line. James, a maintenance technician at the facility, uses this intel to proactively schedule maintenance, and replaces the corroded section before it leads to a catastrophic failure. The facility avoids unplanned downtime, saving both time and resources.
III. Maintenance Cost Reduction:
A. Mitigating Emergency Situations:
Updated piping schematics enable facility managers to stop emergency situations before they escalate into full blown catastrophes, quickly addressing any issues that may arise utilizing the accurate and up-to-date information on the schematics. By having the system resurveyed periodically, facility managers can be proactive in their repairs, avoiding emergency replacements and reducing overall maintenance costs.
- Timely identification of deteriorating conditions prevents emergencies.
- Avoiding emergency repairs reduces overall maintenance costs.
- ROI Example: Emily, the Plant Manager: Emily, a plant manager, receives notice from the contracted surveyor that there is a deteriorating pipe in a critical production line. By proactively replacing the compromised section, she prevents a catastrophic failure that could have resulted in significant downtime and production losses. The cost of planned maintenance is significantly lower than the potential losses from an emergency shutdown.
B. Minimizing Production Downtime:
Updated schematics empower facility managers to plan maintenance during scheduled downtimes, minimizing the impact on overall production. Unplanned downtime due to piping failures is reduced, ensuring continuous operation.
- Proactive maintenance minimizes unexpected breakdowns, reducing production downtime.
- Planned shutdowns based on updated schematics allow for efficient maintenance schedules.
- ROI Example: David, the Production Supervisor: David, a production supervisor, collaborates with facility managers to schedule maintenance based on updated schematics during a planned production downtime. The production line is back up and running as scheduled, avoiding unexpected halts and maintaining optimal production efficiency. The facility experiences increased revenue by adhering to production timelines.
Conclusion:
In conclusion, the strategic advantage of periodically updating and digitizing piping schematics extends far beyond mere documentation. It serves as a powerful tool for understaffed facility management teams, offering remote navigation capabilities, proactive planning, and substantial ROI through cost savings and operational efficiency gains. By detecting and addressing piping condition problems before they escalate into emergencies, periodically updating piping schematics with onsite surveys plays a pivotal role in ensuring uninterrupted production and maintaining the overall health of industrial facilities. Embracing this approach not only mitigates risks but also positions companies for sustained success in the competitive manufacturing and industrial landscape.