Summary
In large food processing plants, piping systems are the lifeblood of daily operations, transporting water, chemicals, and other essential fluids. However, piping system inefficiencies can quickly disrupt workflows, increase operational costs, and lead to safety hazards. At our plant, we realized these inefficiencies were affecting production quality and regulatory compliance. To tackle the issue head-on, we launched a comprehensive piping system survey, followed by the creation of accurate schematics and a dedicated database for ongoing monitoring.
This effort was key to identifying and addressing a range of critical issues that had long gone unnoticed. Here’s how we transformed our operations by identifying and fixing our piping system inefficiencies.
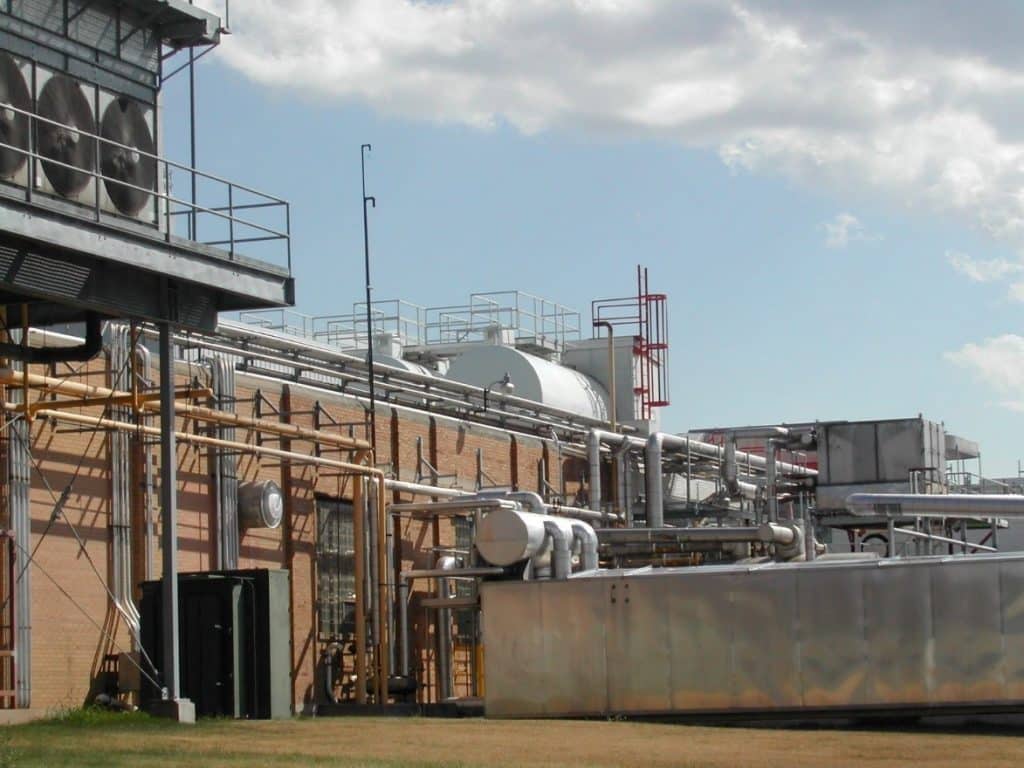
Identifying Piping System Inefficiencies Through a Comprehensive Survey
The first step in solving our piping system inefficiencies was conducting a full-scale survey. Our facility’s piping network is vast and complex, so we brought in specialized technicians to map out every pipe, valve, and connection. This thorough evaluation uncovered several problems that had been plaguing our plant for years.
- Lack of Redundancy in Critical Piping
- Some of our most critical piping lines lacked redundancy, leaving the entire system vulnerable to shutdowns if one line failed.
- Unsafe Cross-Connections
- We discovered several cross-connection issues that could have led to serious health risks and regulatory fines. Ensuring compliance with cross-connection control regulations is essential in the food processing industry, but these issues have slipped under the radar.
- Mislabeled or Missing Valves
- Misidentified or unlabeled valves were creating confusion during shutdowns and maintenance procedures. This increased downtime and complicated emergency responses.
- Corrosion in Aging Piping
- Corroded pipes posed a serious risk of leaks and contamination. Many sections of our older piping were compromised, leading to inefficiencies in fluid transport and posing a contamination risk to our production lines.
- Pressure Imbalances in the System
- Pressure imbalances, caused by improperly calibrated pumps or clogged pipes, were another major contributor to our inefficiencies. The imbalances not only reduced system performance but also put undue strain on our equipment.
- Water Flow Restriction Due to Scale Build-Up
- Scale build-up inside pipes was restricting water flow, making our system work harder than necessary. This inefficiency increased energy use and strained our water pumps.
- Undetected Leaks
- Our survey revealed several undetected slow leaks, leading to wasted water and increasing the risk of contamination.
- Inadequate Pipe Insulation
- Pipe insulation problems were causing significant energy losses and condensation issues, which can lead to corrosion and system failures over time.
- Pump Cavitation from Incorrect Flow Rate
- Incorrect flow rates were causing cavitation in some pumps, leading to noise, inefficiency, and premature wear.
- Inaccurate Metering of Water Consumption
- Outdated and faulty meters meant we were unable to track our water usage accurately. This hindered our ability to monitor consumption and optimize efficiency, further contributing to system inefficiencies.
Solving the Issues: Creating Piping Schematics and a Centralized Database
After the survey identified these inefficiencies, we took the next logical step: creating detailed, up-to-date piping schematics. These schematics accurately mapped every pipeline, valve, and connection point in the facility. With these schematics, our team now has a clear and precise reference for daily operations, maintenance, and emergency situations.
In addition to the schematics, we implemented a centralized database to manage the entire piping system. This system allows us to monitor key metrics such as flow rates, pressure levels, and water consumption in real time. By linking our meters and sensors to the database, we now have full visibility into the state of our piping infrastructure.
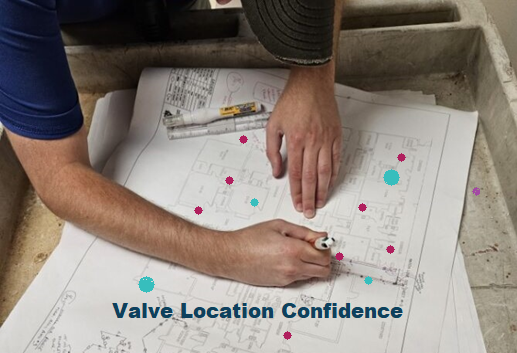
The Impact of Addressing Piping System Inefficiencies
Since taking these steps, the impact on our operations has been profound:
- Corrosion Control: By replacing corroded sections and implementing corrosion-resistant materials, we’ve extended the lifespan of our pipes and minimized the risk of contamination.
- Improved Valve Management: With accurate labeling and documentation, we can now quickly locate and manage valves, reducing downtime during maintenance and emergency shutdowns.
- Pressure Monitoring: Our new monitoring system provides real-time pressure data, ensuring balanced flow and reducing strain on equipment.
- Scale Build-Up Prevention: Routine pipe cleaning and the use of a water softening system have significantly reduced scale build-up, improving water flow and efficiency.
- Redundancy in Critical Lines: Adding redundant piping in critical areas means we can now perform maintenance or handle unexpected failures without disrupting operations.
- Advanced Leak Detection: With our new leak detection system, we’re immediately alerted to any leaks, allowing for fast repairs and reducing water waste.
- Cross-Connection Compliance: Regular cross-connection control testing and monitoring ensures compliance with industry regulations and keeps our potable water systems safe.
- Enhanced Pipe Insulation: Improved insulation has reduced energy losses and prevented the condensation issues that lead to corrosion.
- Optimal Pump Performance: By adjusting flow rates, we’ve eliminated pump cavitation, extending the life of our equipment and improving overall system performance.
- Accurate Water Metering: Upgraded meters allow us to track water usage accurately, helping us optimize resource consumption and reduce costs.
A Proactive Approach to Piping System Efficiency
Addressing piping system inefficiencies in a large food processing plant is no small feat, but the benefits far outweigh the effort. By conducting a thorough piping survey, creating detailed schematics, and implementing a centralized database for real-time monitoring, we’ve not only solved existing issues but also future-proofed our operations.
For any facility looking to boost efficiency, reduce downtime, and maintain regulatory compliance, focusing on piping system management is essential. Our experience has shown that a proactive approach to managing piping systems pays off in increased operational efficiency, cost savings, and improved safety.
By addressing our piping system inefficiencies, we’ve not only improved our daily operations but also set ourselves up for continued success in the competitive world of food processing.